PTFE Dry Film Mold Release Agents
Superior Lubricity and Anti-Stick Properties, Ultra Thin-Films, No Post-Molding Cleaning
PTFE (polytetrafluoroethylene) is a robust fluoropolymer which exhibits excellent chemical and thermal stability, high lubricity, low coefficient of friction, and functions as a premier mold release agent. Miller-Stephenson takes the application of PTFE Dry Film Mold Release Agents a step-further and utilizes a proprietary ultra-low molecular weight PTFE polymer to yield unsurpassed adhesion to mold surfaces, maximizing durability while minimizing coefficient of friction. Our next-generation formulations provide superior thin-film coatings ( 5-12 µm) while offering unmatched anti-stick and release properties. These attributes translate to the virtual elimination of mold part distortion – an extremely important criterion in precision molding. Our PTFE dry film release agents are not only ideal for mold release applications but also for dry lubricant operations. Benefits of Miller-Stephenson PTFE Dry Film Release agents:
- Unparalleled release agent durability and surface adhesion
- Superior Lubricity and Anti-Stick Properties
- Ideal for Rubber-to-Metal Bonding; Silicone molding
- Ideal for Epoxy, Composite and Plastic Substrates
- Excels at difficult mold geometries
- Non-migrating; Non-staining
In comparison to typical release agents such as waxes and silicone oil-based release agents, PTFE minimize the need for post molding cleaning, allowing ancillary processes such as painting, adhesives, etc to be done immediately. These post-molding processes are often not directly compatible with the use of a silicone or wax-based release agents. If the release agent contains silicone, then painting or gluing the component directly after molding will not be possible because silicone residue that remains on the component does not allow paint or adhesives to bond with the component. Miller-Stephenson’s exclusion PTFE Dry Film Mold Release Agents resin provides not only superior release ease but also a 100% paintable surface. This results considerable savings as no time intensive cleaning steps are required prior to painting, gluing or bonding your molded part.
PTFE Dry Film Mold Release Agents | Robust Performance, Ease of Application, Predictable Release – a potent combination
Silicone-based release agents will cause the surface of parts to seem oily or will “stain” the molded part. Silicone is difficult to remove from various material surfaces once it has become integrated into the mold part, and typically the part will scraped. The risk of operation contamination is also very high and free silicone can shut down a manufacturing paint shop fairly easily, causing production delays and incurring significant expense.Miller-Stephenson has developed a robust portfolio of PTFE Dry Film release agents which circumvent all the drawbacks of silicone oil and wax-based release agents, while also increasing the application efficiency and cost-effectiveness. The use of silicone-free release agents allows for the removal of costly and time consuming cleaning steps and cross-contamination risk in the manufacturing process of many components, thus increasing productivity and lowering operational costs.
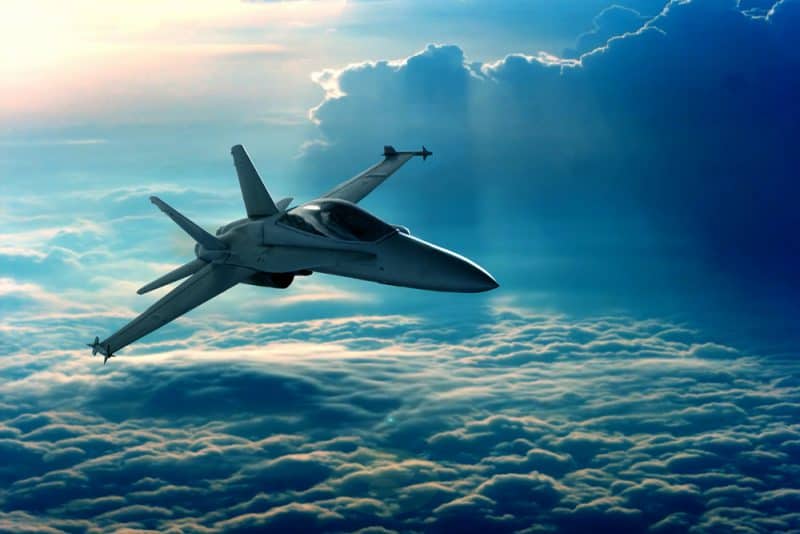
Our PTFE Dry Film Mold Release Agents generate a dry film on the mold surface, which is chemical inert, non-migrating and non-staining. Formulations for this class of mold release agent can be solvent or water-based and application is typically performed with brushing or aerosolization. Once the solvent is dried, the release coating is ready for operation, no additional cure time is needed. PTFE dry film release agents are particularly useful in rubber-to-metal bonding operations or when molding silicone or fluorosilicone polymers and elastomers. Customers have found invaluable utility in utilizing Miller-Stephenson PTFE for electronic resin potting and casting operations. PTFE, in general has exceptional utility and can be use in compression and transfer molding operations, however due to its relatively low slip, it can be ineffective with injection molding operations. Production engineers will typically choose PTFE-based release agents if they are looking for a non-silicone, chemical inert, and non-transferable release agent that is applicable across a broad range of substrates. PTFE, on a release per application basis is significantly more efficient and cost-effective than sacrificial or PVA alternatives. Miller-Stephenson’s MS-122AV, ReleaSys DFX and ReleaSys™ DF are formulations which increase the durability and cost-effectiveness even further by addition of proprietary surface activation chemistry. To learn more about our mold release agents please click here.For further reading about non-silicone based release systems continue our articles about the topic.
Technical or Application Support:
- For any questions about proper application of our mold release products please view our article which discusses this process
- If you require any further technical or application support please contact our technical staff
Notwithstanding any express or implied indication to the contrary, product information provided on or via this website is supplied upon the condition that the persons receiving such information will make their own, independent determination as to a given product’s suitability for any contemplated purposes prior to use. In no event will Miller-Stephenson be responsible for damages of any nature whatsoever resulting from the use of, or reliance upon, information provided, directly or indirectly, on this website in relation to any product and/or application.